Pilot Experiments
ARCO: Augmented Reality and Cobots for the Digital Transformation of the Cable Manufacturing Industry

Experiment objective
OBJECTIVE 1: DEVELOP AND VALIDATE AN AUGMENTED REALITY APPLICATION FOR MAINTENACE OF A CABLE PROCESSING MACHINE AND TRAINING-ON-THE-JOB
The cable assembly industry still largely depends on manual work, a reason why it is still mainly rooted in cost-effective labour countries. The introduction of more automation in the cable assembly factories is facing challenges not only due to the lack of qualified technicians but also to the complexity and diversity of the cable processing machines designed to replace meticulous manual work. In fact, maintenance workers in these factories are faced with daunting challenges to understand operation and maintenance routines to keep machines running and functioning efficiently.
In this context, the first objective of this experiment is to bring into the real work environment, an enhanced Augmented Reality (AR) application for training-on-the-job and assist maintenance operations of industrial machines manufactured by STONESHIELD for the cable assembly industry. By using our AR application, a maintenance worker in a remote factory (e.g., in Egypt), can pull up to a job site with a pair of AR glasses (or a tablet), and have at his disposal every piece of information necessary to perform their task (operating and maintenance tutorials and procedures, schematics, documentation, logs, alerts from IoT sensors, etc.). The same AR application will also enable the worker to connect live to a remote technical service agent (in Portugal) to provide support through a specific issue or a particularly difficult activity.
The ability to see information overlays on top of the machine, combined with information from industrial sensors and Machine Learning analytics, has the potential to completely transform the areas of training and maintenance in the cable assembly industry. This will ultimately lead to a more motivated worker, increased operation safety, lower service costs, higher equipment availability and extended equipment lifetime.
OBJECTIVE 2: DEVELOP AND VALIDATE A HUMAN-ROBOT COLLABORATION SYSTEM FOR A FUSE BOX ASSEMBLY PROCESS
An important component of an automotive harness is the fuse box. Fuse boxes need to be correctly assembled to protect against overcurrent of the car electrical circuits. It is, therefore, essential to ensure the correct fuses are in the right places. Manufacturing workers who are accustomed to performing repetitive tasks with the same movements over a long period of time can still make mistakes when pressured by the production timelines or goals, to perform their tasks faster for higher production outputs. It is essential to alleviate monotonous work whilst ensuring flawless assembly.
In this context, the second objective of this experiment is to showcase that a manufacturing worker can benefit from human-robot collaboration (COBOT) in the assembly process of different fuse boxes. For each fuse box, the robot will recognize the layout to use, and know which fuses it will be required to assemble. The robot working zone will be dynamic and projected onto the fuse box assembly station. The robot and worker will function as members of the same assembly team. This experiment will make use of computer vision based on Object Classification and Object Detection algorithms (using deep Convolutional Neural Networks). At the end of each assembly process, the robot will inspect each fuse box and issue a ‘PASS’ or ‘FAIL’ status.
Challenges
Automaker industrial plants are excellent examples of state-of-the-art robotization and agile production. Car manufacturers are supplied by a range of second line industries that produce many of the components integrated in vehicles. Despite all the automation of car production, the second line industry responsible for supplying the wiring harnesses (electric cables) is still depending on considerable manual processes, therefore, most cable assembly factories are located in cost-effective labour countries such as Mexico (with more than 400 factories), Morocco, Tunisia, Egypt and India. Portugal also has some cable assembly factories. However, due increasingly stringent quality requirements, together with the demand to lower production costs and miniaturization, there is now a strong push towards automation and robotization of the cable assembly processes.
Understandably, the complexity and diversity of the cable assembly processes that needs to be automatized to replace meticulous manual work requires state-of-the-art collaborative robotics, computer vision, IoT and new training and maintenance tools. Such transformation is a major challenge for the manufactures of cable processing machines and requires new knowledge and competences on novel robotic solutions. STONESHIELD, a robotic integrator, has been challenged by IPCB, a technical university and DIH to joint efforts to take advantage of this need and market opportunity.
Implementation Solution
PART 1 – AR APPLICATION FOR MAINTENACE OF A CABLE PROCESSING MACHINE AND TRAINING-ON-THE-JOB
The AR application will provide step-by-step digital work instructions for the successful configuration and maintenance of a Connector Robotic Assembly Machine manufactured by STONESHIELD.
PART 2 – HUMAN-ROBOT COLLABORATION FOR A FUSE BOX ASSEMBLY PROCESS
This experiment will use the OMRON TM5-900 collaborative robot to assemble fuse boxes. The operation takes place in an assembly station, as depicted in Figure 3. Moreover, this experiment will demonstrate a 3D vision-based safety system where a dynamic 3D map of the working environment (robot, components, and humans) is continuously updated, increasing safety and speed of the Human-Robot collaboration process.
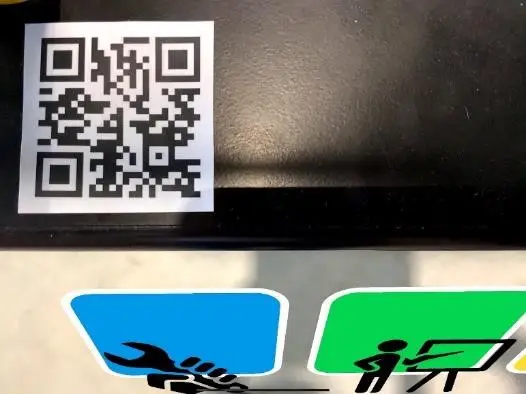
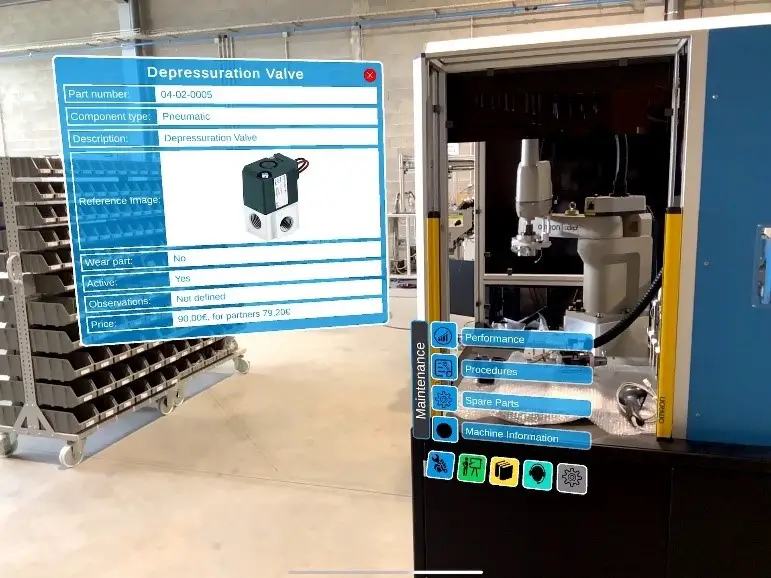
Results Obtained
PART 1 – AR APPLICATION FOR MAINTENACE OF A CABLE PROCESSING MACHINE AND TRAINING-ON-THE-JOB
The transition of the traditional training processes (dedicated training in customer premises, hands-on training, and paper manuals) to a digital AR training process has considerably reduced the amount of time and investment required to train new RoSI maintenance technicians. It was demonstrated a minimum of 50% decrease on the average time required to train a maintenance technician to correctly perform an unfamiliar, or new, maintenance operation on a cable processing machine, thanks to our AR-based application with step-by-step digital work instructions
Moreover, using our remote video assistance support, built within our AR application, we estimate a significative reduction in the number of trips to provide onsite maintenance operations, meaning an average cost savings of 70% in maintenance operations of cable assembly machines for STONESHIELD. This is an important economic incentive for the adoption of AR and remote maintenance technologies.
PART 2 – HUMAN-ROBOT COLLABORATION FOR A FUSE BOX ASSEMBLY PROCESS
The fuse box named APN001 (in blue) is for robot assembly only, as it is beyond the projected safety line (white horizontal line). The other fuse boxes (APN0002 and APN003) are for collaborative assembly. Besides the safety line projection, the safe area for the worker is highlighted in bright white light, whilst the area dedicated for robot assembly is highlighted in bright yellow light.
The core goal of this demonstrator was to achieve up to 30% decrease in the assembly process of fuse boxes. The values obtained for this KPI depends on the fuse box layout and the percentage of work given to the worker. For this demonstrator we tested a total of 4 different fuse box layouts.
Depending on the fuse box layout different percentages of work need to be given to robot to achieve maximum gains in the collaborative operation. A KPI of 30% decrease in the assembly process of fuse boxes, has been achieved.
In four of the seven scenarios, the robot finishes the work before the human worker (this is because in our setup relays are only placed by humans), if additional fuse boxes (layout d) are made available on the assembly station for robot assembly, the robot will continue to work on those fuse boxes, until the worker starts a new collaboration order, increasing the overall gain of the system.
The overall results of the ARCO experiment have suppressed the expected KPIs planned at the beginning of the experiment.
Impact of the experiment
AR IMPACT:
Decrease of the average time required to train a maintenance technician to correctly perform an unfamiliar, or new, maintenance operation on a cable processing machine, using step-by-step instructions by an AR application
Decrease the average cost in maintenance operations of cable assembly machines using remote support by an AR application.
COBOT IMPACT:
Decrease of the cycle time of a car’s fuse box assembly process, thanks to human-robot collaboration with dynamic 3D safety zones
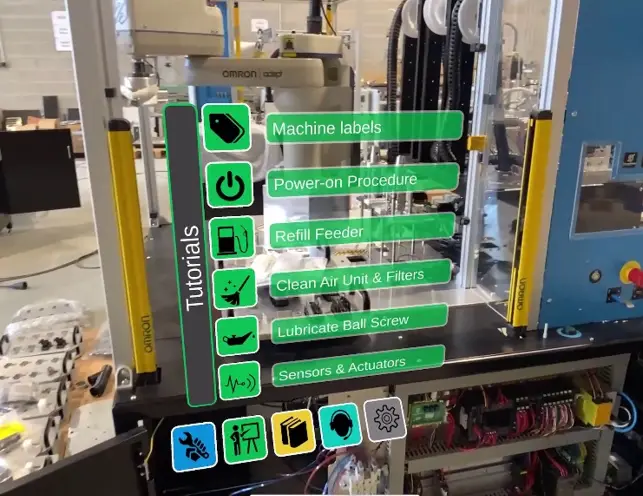
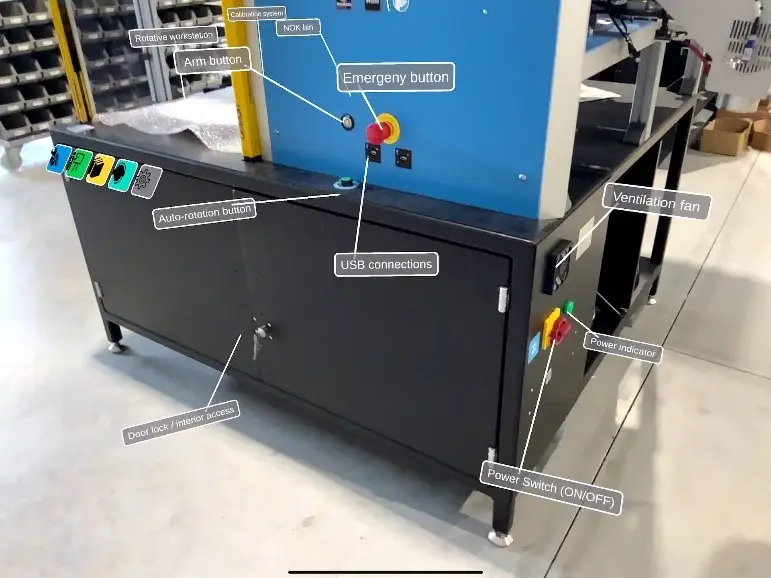