Experiments
Deep lEarning for automatiC tExtile iNspecTion (DECENT)
Spain, Cantabria
DIH on Livestock, Environment, Agriculture and Forest (DIH-LEAF)
Experiment objective
The main objective of the DECENT experiment is to validate AI models, Deep Learning (DL) Architectures more precisely, for the automatic detection and identification of fabric defects. INADE, as a technological services provider for TS Group pursues the integration of DL, Image Capturing and Processing (ICP), and Edge Computing (EC) in the manufacturing process to support an early and accurate detection of a wide variety of flaws that are often present in textile products manufactured at present time. It will have a benefit on INADE (as a provider of technological services) and on the TS group as it will allow inspection for defects to take place 24/7 at the precise place of manufacture, minimizing human intervention and expanding the coverage of detected defects. Likewise, the full integration of the DECENT solution with the production machinery will allow defects to be recorded and identified at all times, gathering historical information, location and trajectory of defects and products

Fig. 1: Fabric defect
Challenges
The present innovative experiment aims at applying some of the Key Enabling Technologies (KETs) for Industry 4.0 (AI, Cyber Physical Systems, and Sensors) in the textile manufacturing of Textil Santanderina (TS) group. In particular, some KETs are to be applied to automatically control the quality of fabrics in order to identify defects (warp and weft defects, impurities, bow, skew or colour gradients) generated at any of the process stages (spinning, weaving, coating finishing, and garment manufacturing) in any of the different branches of business with their particularities in terms of quality control (fashion and garments, personal protective equipment, sports and leisure, automotive fabrics, etc.).
This could be done by INADE as it is part of TS group, currently being the only company in EU that gathers in the same facility (15,000 m2) all the phases of fabric manufacturing, from spinning to finishing, including weaving, preparing, dyeing and/or screen printing. This superb level of integration and coordination let the company to supply a high amount of different processed products at any stage of production, with any type of finishing. As a result, more than 700 new references of different products are manufactured by TS per year. The DECENT solution will be applied to all kinds of fabrics that TS manufacture (from fashion to automotive industry
Currently, the inspection process in TS is carried out through visual inspection by qualified workers (specifically trained). It is done for every single meter of fabric produced (average speed about 20 m/min) and random quality checks are carried out every 5,000 m produced. The manufacturing speed of the different production lines is around 42 m/min, so the quality inspection phase is a bottleneck. Although being satisfactory so far, the textile manufacturing industry is evolving, with increasing demand for products and quality, with a parallel increase in manufacturing speeds. Hence, traditional visual inspection is becoming obsolete, with drawbacks demanding innovative and solutions, as the DECENT one.
Implementation Solution
The main innovations of the DECENT solution are:
- Hardware: the elements that allow to visually inspect the textile in real time, capturing images of the product, will be integrated. The pictures will then be transmitted to an EC device for online processing, that will send early warnings in order to minimize the consequences of the found defects.
- Software: the DL methods will support automatic detection, classification and counting of found defects, as well as error reporting. From the DL side of the experiment, the following innovative aspects are worth mentioning:
- As the inspection will be applied at different stages of the production process, tailored-made DL models will be generated for each one of the manufacturing stages.
- Although there is a huge amount of defects that will be available for training, and properly labelled (in most cases) by TS staff, few samples will be available for some of the defects that scarcely happen. In order to balance the datasets, additional samples of such defects will be found and incorporated, optimizing the used resources thanks to active learning.
- Transfer learning will be considered in an innovative way. Pre-trained DL models (Alexnet, VGG19, Inceptionv3, YOLOv5, and ResNet50 among others) will be fine-trained on the DECENT dataset. Additionally, new CNN architectures will be pre-trained on open textile datasets (such as the TILDA Textile Texture-Database ) and then fine-trained on the DECENT dataset. The classification performance of both approaches will be compared.
The software tool to be applied for the image processing is OpenCV (https://opencv.org) while for the DL models TensorFlow (https://www.tensorflow.org) and Keras (https://keras.io) have been selected due to the technological ecosystem where the digital solution will be integrated. With such tools, Deep Neural Networks will be trained on the acquired images, according to the standard procedures of training, testing and validation. More precisely, Convolutional Neural Networks (CNNs) are initially proposed due to their superior and widely-validated ability to process images and classify them. Different topologies of such architectures will be benchmarked in order to identify the one best fitting the problem under analysis. Furthermore, the classification performance of pre-trained CNNs will also be explored and compared.
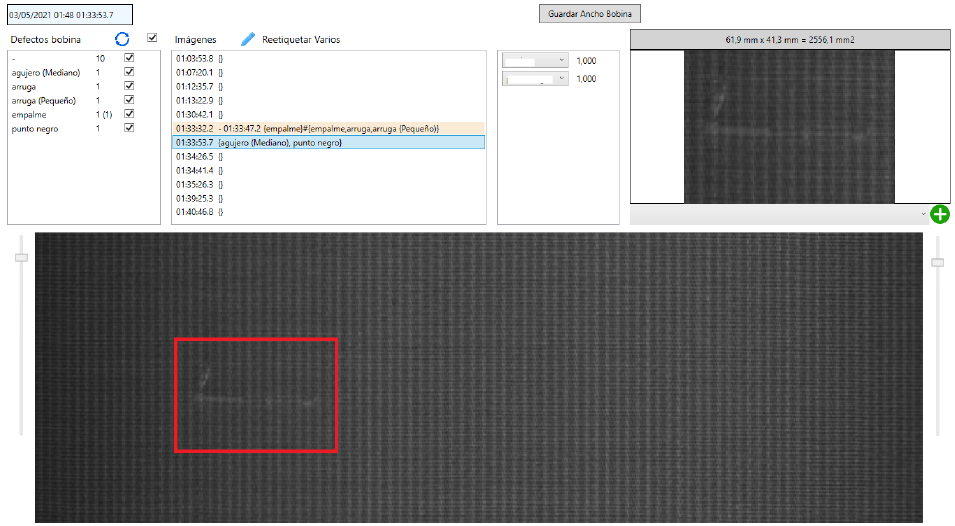
Fig. 2: Defect recognition.
Results obtained
The main defects have been categorized and defined. Statistical analysis has been carried out in the defect database of the TS group in order to define the frequency patterns of each one of them in the different manufacturing facilities.
Impact of the experiment
DECENT will increase the competitive advantage of TS group in a sustainable way, generating the following benefits:
- Increased quality: uninterrupted inspection, quality monitoring and identifying defects in real time will be achieved. This would imply that the products in the TS portfolio will meet the highest quality standards and ensure greater flexibility and a much faster response to the different demands imposed by its customers.
- Improved productivity: the new solution will have a positive impact on the primary processes of the value chain; (i) optimizing manufacturing times, reducing the times associated with production stoppages, and quickly addressing production setbacks; (ii) guarantee compliance with delivery times by optimizing manufacturing times and reducing production stoppages, (iii) eliminating production bottlenecks, while minimizing the need for reprocessing.
- Increased process and product traceability: the traceability of the product (in time and location) and of the detected defects will be guaranteed. Every error will be accurately identified and reported.
Finally, the DECENT solution will launch and consolidate INADE as one of the most suitable providers of technological services for quality inspection in fabrics in EU. This will open a door for INADE to a new international market branch beyond the limits of TS group, either alone or as a partner of specialized machinery manufacturers.

Fig. 3: Kick-off Meeting.