Experiments
DRITTO – Deflection Reduction In Turning by Toolpath Optimization
Italy, Tuscany
ARTES 4.0
Experiment objective
The DRITTO experiment targets the machining sector, in which Meccanica Ceccarelli & Rossi provides services as contractor to different customers. DRITTO aims at developing an easy-to-use digital twin-based solution to support manufacturing (i.e., turning) of slender axisymmetric components, taking the most out of the advanced simulation tools to automatically compute close-to-optimal machining cycles, without requiring additional expertise on the operator side nor time-wasting trial and error procedures. In order to achieve such demanding goals, the development of a black-box (i.e., automated) toolpath optimization solution will be required. The direct and indirect objectives of DRITTO can be summarized in:
- Digitalization: Developing a tailored digital solution for the machining of flexible axisymmetric components;
- Worker Empowering: Reducing the trial and error repeatable procedures and enhancing the digital skills of operators, with an easy-to-use solution to support the definition of turning cycle of slender components;
- Sustainability: Developing optimal turning toolpaths for slender components, right at the first time, reducing scraps or re-machining procedure of about 30%;
- Productivity: Shortening manufacturing lead time by at least 20% and improving product quality.
DIH Matureness: Increasing the Digital Innovation Hub partner (ARTES 4.0) expertise, strengthening its capacities and international collaborations
Challenges
The Main Challenge addressed by the DRITTO experiment and provided by the SME Meccanica Ceccarelli & Rossi (MC&R) is the first-time right manufacturing of slender axisymmetric components using turning, avoiding time-consuming trial and error procedures and minimizing scraps. Such challenge could be overcome by exploiting digital solutions able to predict slender components behaviour during machining process and compute an optimized toolpath. To achieve such goal three Technical Challenges (TCs) need to be addressed.
- Challenge 1: Workpiece FE modelling. Estimating the workpiece behaviour during the turning process will entail considering the effects of the material removal, since the workpiece geometry will continuously change during the process. Different modelling strategies (e.g., beam 1D, shell 2D, solid 3D) will be investigated to identify the one providing the required accuracy and better suiting the integration. Self-developed algorithms, open source or commercial FE solver will be evaluated to fulfil these requirements.
- Challenge 2: Turing process forces. Several methods exist to estimate the cutting forces generated in the turning process. Selecting the most suitable model to be implemented in the DRITTO solution will entail analysing, implementing and testing/validating alternative approaches. Dedicated algorithms will be developed to geometrically estimate the instantaneous chip thickness, achieving the best trade-off between accuracy and computational efficiency.
- Challenge 3: Suitable toolpath optimization. Once the workpiece deflection is estimated, a suitable compensated toolpath shall be generated. This compensation could be computed either by post-processing the original machining cycle or by intervening during the toolpath generation. Once again, the selection of the optimization algorithm will be driven by both effectiveness and computational efficiency.
MC&R will be supported by ARTES 4.0, technology provider and Digital Innovation Hub (DIH) from the same region (i.e., Tuscany, Italy) to develop and integrate the digital prototype in its process and validate its effectiveness.
Implementation Solution
The proposed digital solution, starting from a non-optimized toolpath, stock and finished geometries and tool parameters, will compute an optimized toolpath by integrating three different modules: a) workpiece FE modelling, b) turning process modelling, c) toolpath optimization.
The first module automatically generates and updates the workpiece FE model, while the second one is the digital twin of the turning process, which is in charge of computing cutting forces by considering tool-workpiece materials and their relative position. The toolpath computation (module c) will be performed taking into account the actual workpiece compliance, that changes during the turning process, as a consequence of material removal (module a), and the instantaneous cutting conditions (module b). At each time-step, the workpiece geometry will be modelled and updated, and a FE analysis will be performed to compute workpiece static deflection, exploited by the optimization algorithm to derive the suitable machining cycle that minimizes the geometrical errors.
All the modules will be validated individually and as whole by dedicated experiments at MC&R.
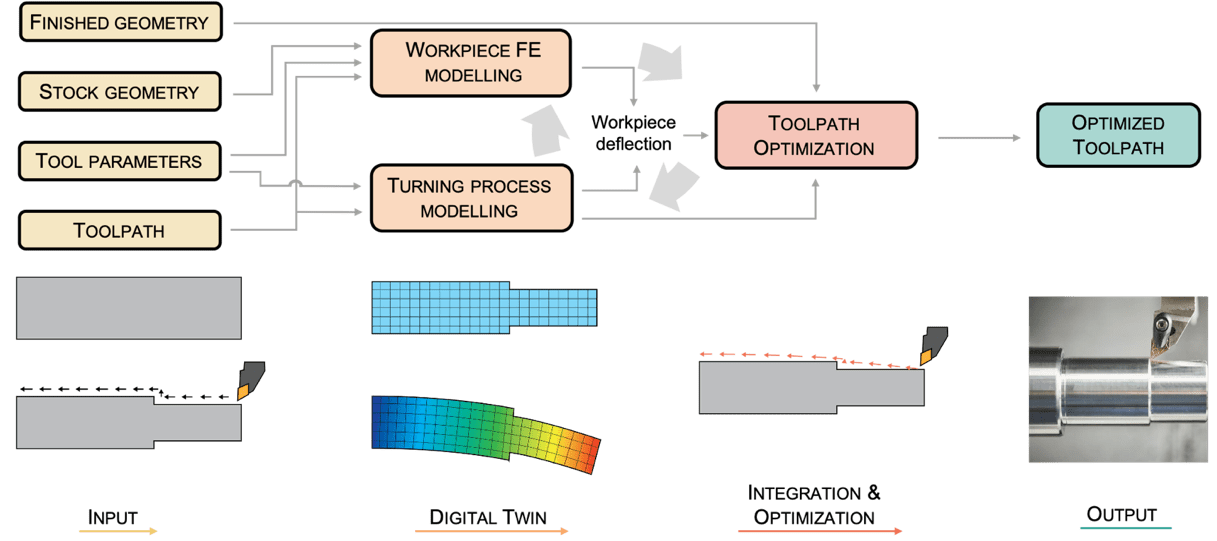
Your Title Goes Here
Figure 1 DRITTO digital solution concept