Experiments
WALCHY (Wire Arc Additive technologies for Pressure Hydrogen valves components)
Italy, Lombardy, Piantedo (SO)
Polytronics
Experiment objective
Hydrogen represents one of the most promising alternatives to fossil fuels to support EU energy transition towards a decarbonized Europe meeting COP21 and EU Green Deal target. Hydrogen global demand is expected to grow by 74% (ca 270 MtH2 per year) until 2050, driven by a cross-sectoral demand with Oil&Gas representing 70% of it. With production costs falling, hydrogen infrastructure, maintenance and transport costs are the main bottleneck for hydrogen industry competitiveness. Specifically, transmission and distribution pipelines will include relevant number of valves by 2040, where each valve is typically placed 8-30 km. Hydrogen pipelines network is expected to reach 39.700 km by 2040, with 75% of its length composed by existing retrofitted natural gas. Costs of valve, seal replacements for about 17.000 km of repurposed pipelines alone are estimated to be 690 M€ with procurement and logistic delivery time representing at least 20% of ordinary maintenance delay.
This clearly demonstrates twin transition impact to boost EU components and valves supply chain resilience and sustainability. The experiment leverages 3D printing and recyclability by design approach innovating pressure containing hydrogen valves body component (e.g. valve body) optimizing logistic, procurement phase of energy and hydrogen ordinary maintenance.
Challenges
The updating and retrofitting of the current European energy network presents many potential challenges that make the endeavour costly and time consuming. This project aims to tackle many different challenges implicit in the process by improving the recyclability of components, the production process effectiveness and cost-effectiveness, and technical results, as per the following table:
SPECIFIC Challenge |
KPI |
Decrease production costs |
#1 Manufacturing cost: – 5% #2 Engineering cost: – 10% |
Increase material cost efficiency |
#3 Material procurement cost: – 40% |
Increase satisfaction of customer |
#4 N. of new order: + 10% #5 Customer satisfaction: + 15% |
Increase logistic efficiency |
#6 Time to delivery: – 40% |
Decrease production time |
#7 Lead time: – 50% #8 Engineering time: – 30% |
Increased design by recycling |
#9 Cylinder reuse: + 15% |
Increase quality design |
#10 Product shape quality: + 40% |
Increased material efficiency |
#11 Material use optimization: + 15% #12 Waste metal material: – 35% |
Increase use of recycled metal powder |
#13 Use of recycled material: + 100% |
Increased PhD employed |
#14 N. of PhD in STEM employed: +1 |
Increased international R&I collaboration |
#15 Collaboration with foreign R&D center, tech provider: + 2 |
Increased R&I project |
#16 N. of new international R&D project: +1 |
Challenges linked to materials cost, cost effectiveness, logistic efficiency, recycled material use, production times are linked to the traditional methods of production of the studied components.
Forging is a widely used manufacturing method able to produce strong and reliable parts with high quality material. Machining has the higher cost impact: the billet is not close-to-shape so, many hours are needed to machine the part wasting almost half of the material.
Casting, has a big limit: lead time. Starting point is a model replicating the shape of the final part, and which is used to produce the dye. If the part is completely new or if it needs customization, the model design and production must be included in the overall process with high impact on costs and timing. In this case, close-to-shape parts are produces and so machining is not so meaningful.
In both cases the use of recycled material is strongly limited by the materials cleanliness, quality, chemical composition.
Logistics are also a strong impact due to the fact that both forging and casting require very large industrial complexes dedicated to the working practices involved.
Implementation of the Solution
The project applies Wire-Arc Additive Manufacturing (WAAM) technology to realize the body of a 2” slab gate valve API class 300# dedicated to application in the energy industry.
The experiment consists of the following main steps:
- DESIGN OPTIMIZATION: the present phase will optimize requirements for shape topological optimization and define material requirements. The first step of the process is the characterization of the material produced from the WAAM machine. For this purpose, some specimens will be printed and tested according to the relevant standards for tensile, hardness and impact properties. These values will be used in the design phase and for Finite Element Analysis (FEA) to simulate the capability of the part to withstand pressure and to check that all the possible deformations are kept inside the limits. The design phase is critical to ease the printing phase. Thanks to the high degree of geometrical versatility allowed by the technology, significantly optimized, close-to-shape and lightweight structures can be realized. The geometry will be carefully designed to fit all the safety factors of a pressure containing part but topologically optimized according to WAAM technology characteristics
- PROTOTYPING AND TEST BEFORE INVEST: the present phase includes the body component printing using WAAM technology from external partners and assembled with the other components of the valve. Those will be traditionally manufactured to avoid introducing too high variability in the product and they can be re-designed further on. Finally, the valve with 3D printed body will be tested simulating operating condition for what concerns maximum pressure and sealing capability when exposed to very small particles (such as the hydrogen ones)
INDUSTRIAL UPTAKE. After optimization phase, small scale production will allow for industrial uptake of WALCHY project and preliminary go to market
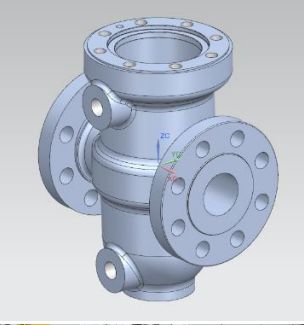
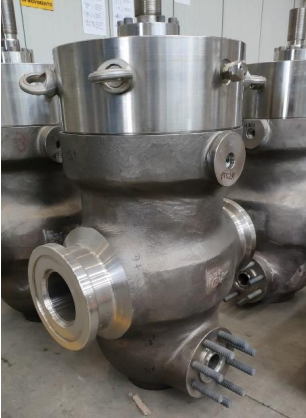